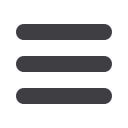
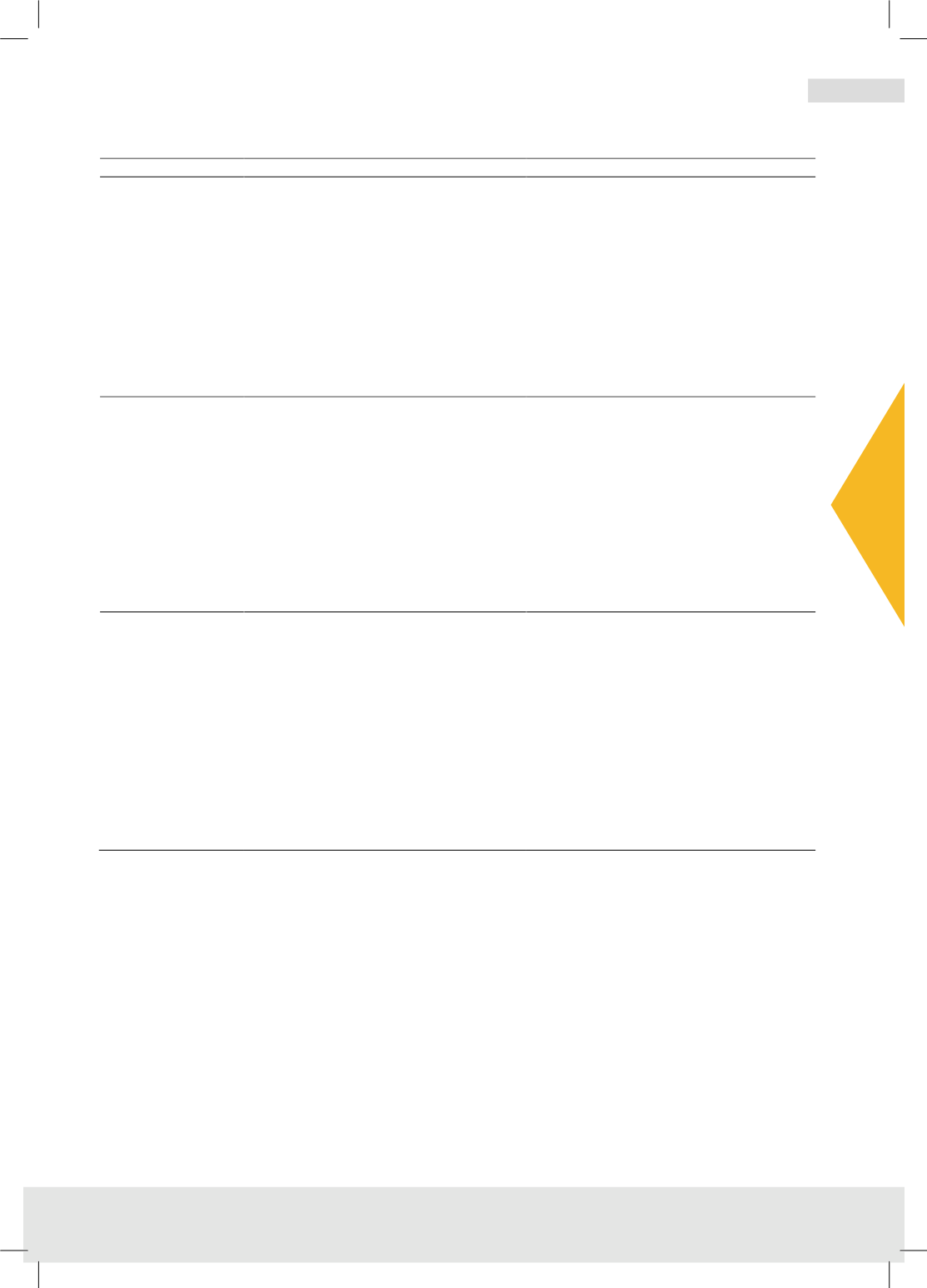
البحـث الثاني
171
2016
أوابك العلمية لعام
�
ص لبحوث العلمية الفائزة بجائزة
�
عدد خا
مجلة النفط والتعاون العربي
161
العدد
- 2017
أربعون
المجلد الثالث و ال
Re-refining of Used Lubricating Oil and its Economic and Environmental Implications
48
Table 4 Advantages and disadvantages of re-refining technologies
Source: Own elaboration. Data compiled from PETDER
Technology
Advantages
Disadvantages
Acid/Clay methods
Low capital investment. Makes it most cost
effective for small and tiny scale plants.
Requires no advanced instrumentation, no
skilled workers.
Proven technology that worked for many
years worldwide
Hazardous by-products are produced,
including acid tar and oil saturated clay.
Waste disposal problems and environmental
drawbacks.
High operation costs, continuous clay
consumption, disposal cost of spent clay. The
process requires high temperatures.
High clay consumption, low yield,
inconsistent quality
Lower yield due to loss of oil in sludge.
Life span of the equipment used in acidic
environment is reduced.
Hydroprocessing
methods
Product quality and yield are high (API
Group II Base Oil),
PBC and Chloride can be eliminated
efficiently
PNA can be eliminated efficiently at high
pressure and temperature
The process requires high pressure, high
temperature and hydrogen usage
It requires high safety standards, H2S and
HCl can be generated during the process
Investment cost and operational costs are
high, operational efficiency is low
A separate facility needs to be established on
the field in order to provide hydrogen to the
process continuously
Expensive catalysts are required
Solvent extraction
methods
API Group II/II+ Base Oil can be produced
based on the quality of the waste oil.
Toxic Polyaromatic Hydrocarbons (PAH)
and PNA can be completely eliminated.
All of the synthetic base oil compounds like
PAO / hydrocarbon oils are preserved,
The process is carried out under lower
pressure and temperature compared to
other technologies.
The process has high product operational
efficiency.
Small quantities of waste and comtaminants
are generated, waste disposal cost is low
The product quality is dependent upon the
waste oil mixture used as feedstock.
High quality feedstock is required for high
quality Group II, Group II+ base oil.
In hydro processing, with hydrogen
saturation, the product quality is not
dependent on the quality of the feedstock.
Based on the waste oil used, the solvent costs
can be high