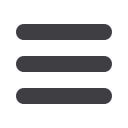
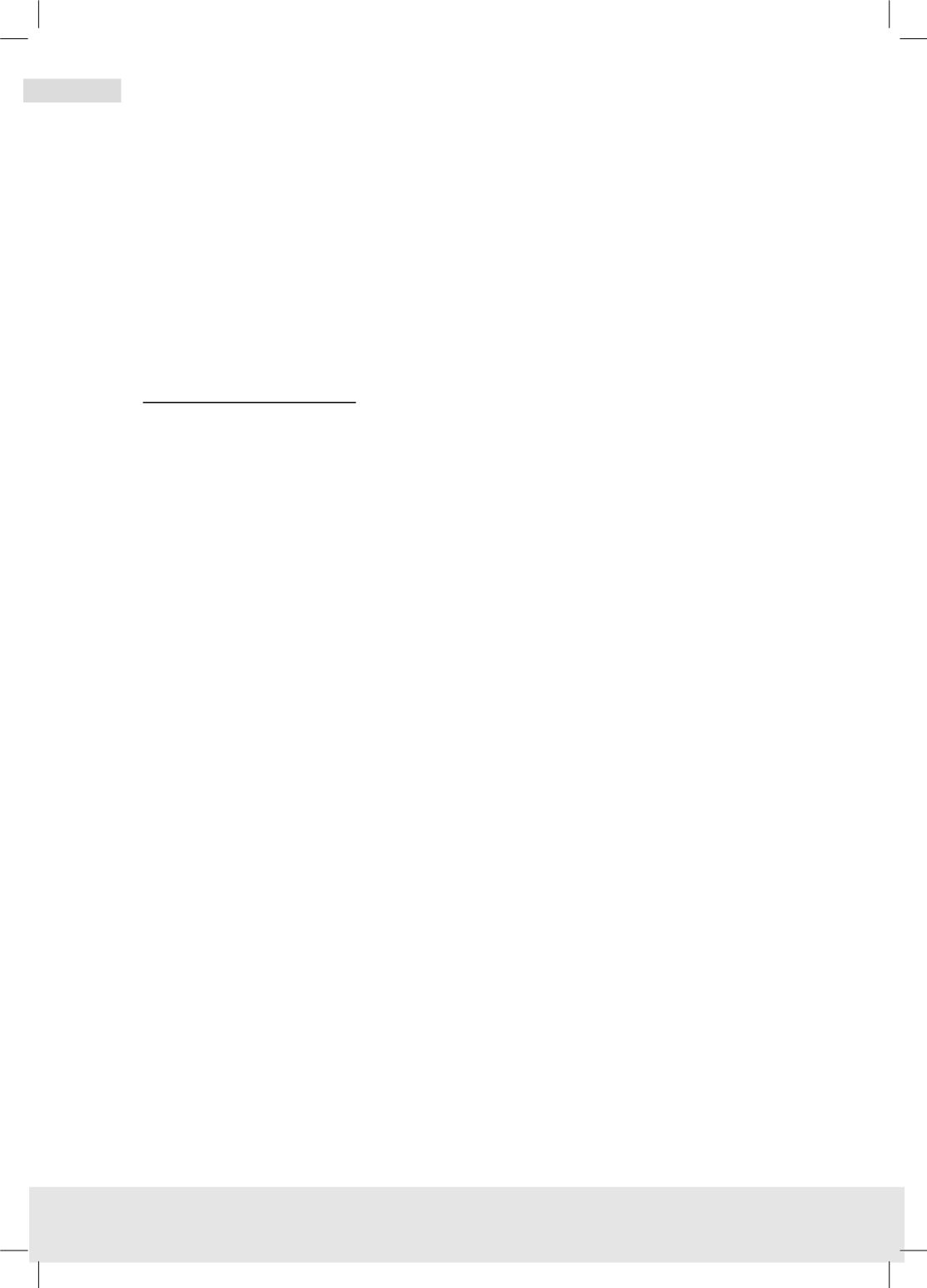
مجلة النفط والتعاون العربي
161
العدد
- 2017
أربعون
المجلد الثالث و ال
2016
أوابك العلمية لعام
�
ص لبحوث العلمية الفائزة بجائزة
�
عدد خا
60
50
The final step is fractionation to recover further gasoil and produce light and
heavy base stocks.
The yields are reported to be 7%water, 5% gasoil, 75% lube oils and 13% asphalt.
Many plants have been built by STP including three in Italy of total capacity 125
thousand tons a year, a plant in Canada of 60 thousand tons a year to produce
VGO and a similar plant in France for 120 thousand tons a year. The company
says that VGO is used as feed for further processing in a fluid catalytic cracking
unit (FCC) or a hydrocracking unit (HC)
94
.
The Dollbergen Process:
1, 24
Fig (14). This process belongs to a re-refinery in Germany (Mimeraol-raffineirie
Dollbergen) and was patented in 2004. It is based on distillation and solvent
extraction processes. After settling and filtration, potassium hydroxide solution
(KOH) is injected into the used oil stream to neutralize acids and help in the de-
metalizing of the oil. The used oil then enters a distillation column at near
atmospheric pressure and 140
o
C to remove water and light ends. The second step
is a vacuum column at bottom temperature of 260
o
C to recover “light heating
oil”
1
, diesel and gasoil, and the third step is a thin film evaporator working under
high vacuum (0.044 psi) and 385
o
C to separate a heavy bottom product. The
stream is then treated by N-methyl1-2-pyrrolidone (NMP) solvent in a solvent
extraction column to extract contaminants and finally to recover solvent and base
oil cuts by distillation.
The processors say that toxic components such as PNA and PCB if present in the
used oil are thereby removed. They claim that the solvent extraction process is
superior to hydrogenation in preserving components of synthetic base oil that may
be present in modern lubricating oils.
A second thin film evaporator under higher vacuum is used to treat the bottoms
of the first one to recover heavier base oil stock (not shown in the diagram). The
base oil yield depends on the solvent to feed ration and can range between 84 and
92%.
The capacity of the re-refinery using this process is 230 thousand tons a year.
24