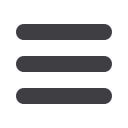
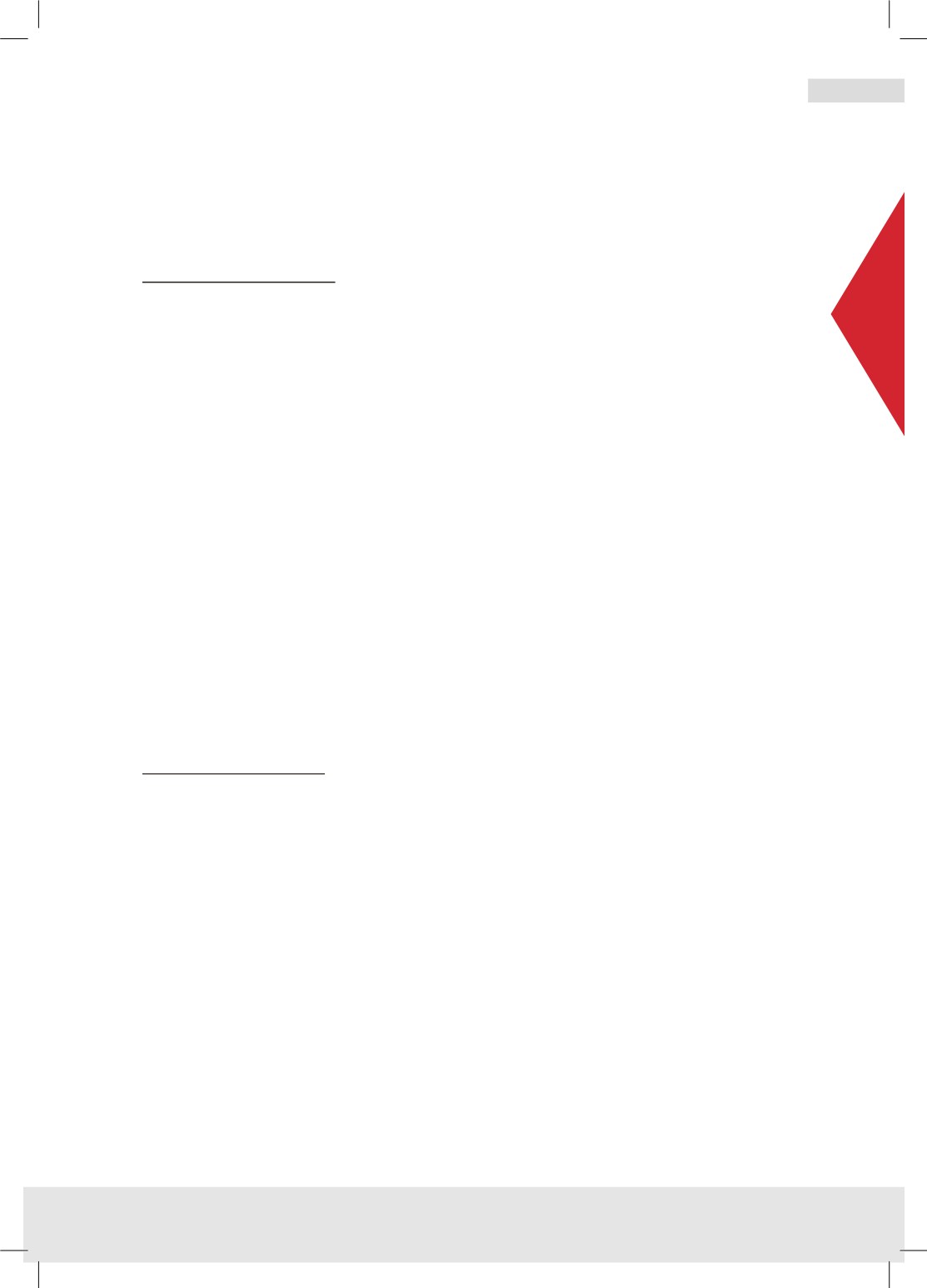
البحـث الأول
مجلة النفط والتعاون العربي
161
العدد
- 2017
أربعون
المجلد الثالث و ال
2016
أوابك العلمية لعام
�
ص لبحوث العلمية الفائزة بجائزة
�
عدد خا
49
39
to 60% because much oil remains with the sludge. The sulphur and polyaromatic
hydrocarbons (PAH) in the oil cannot be separated as contaminants in the oil.
Therefore many countries banned its use though it is still popular in Brazil, China
and India.
The Meinken Process:
1, 3, 107
is is a distillati n/clay treatment process. After settling, filtration and removal
of water and light hydrocarbons in a pre-flash column, 4 to 5% clay is added to
the dewatered oil before wiped-film evaporation under vacuum and 290
o
C to
draw asphalt and contaminants from the bottom and subsequent clay treatment
and filtration of the side cut to finally get the base oil cuts. The process produces
medium quality base oil that still contained sulphur and polynuclear aromatics
(PNA)
1
. Polynuclear Aromatics (PNA) are complex hydrocarbons of many
aromatic rings formed during the use of lubricating oils in severe engine
conditions and some are formed in fossil fuel combustion or cracking processes.
They are classified as carcinogenic which may cause cancer to humans.
No acid is required in this simple process suitable for small capacity plants. But
the high clay consumption, low yield, inconsistent quality and the disposal of
large quantity of spent clay is an environmental problem.
Three plants had been constructed in Germany, one in the United States, one in
Taiwan, one in Brazil and two in Jedah, Saudi Arabia at 10 and 80 thousand tons
a year capacity
1
.
The Sotulub process:
1, 3, 107
Fig (4). This process is developed for Tunisia and patented in France. The used
lube oils are first tested to eliminate stocks of high gasoline, fatty acids and
chlorine. After settling and filtration anti fouling is added to prevent fouling and
blockage of equipment and the feed is heated to 140
o
C and fed to a fractionation
tower to remove water and gasoline and then gas oil is removed in the next
vacuum tower operating at 280
o
C. Finally a vacuum tower stage to produce the
lube cuts as side streams and the bottom is asphaltic residue with all the metal
contaminants.
The last vacuum column can either be replaced with or work with a thin film
evaporator to improve quality of the lube cuts
1
or that the vacuum column and