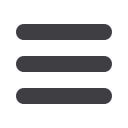
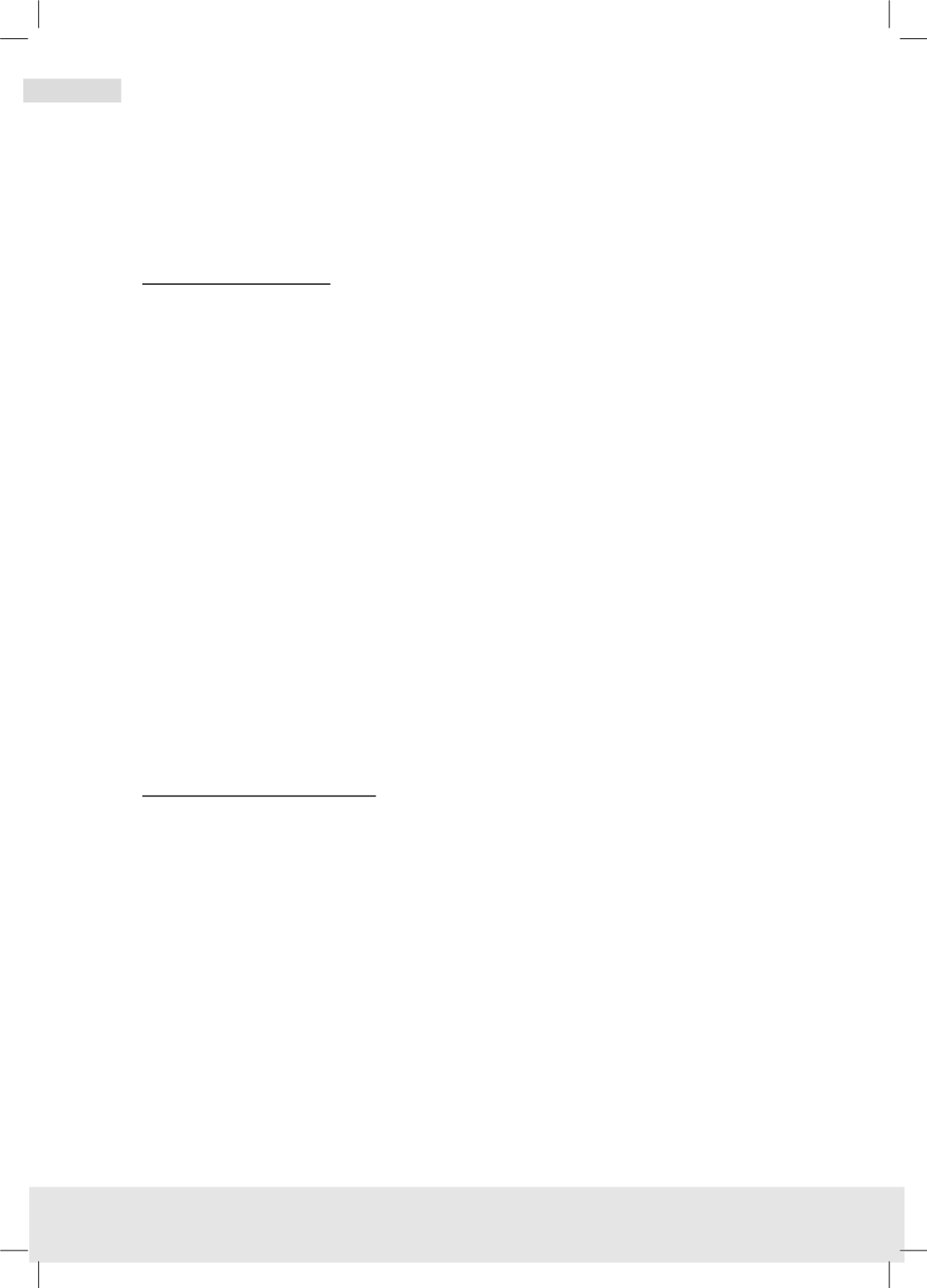
مجلة النفط والتعاون العربي
161
العدد
- 2017
أربعون
المجلد الثالث و ال
2016
أوابك العلمية لعام
�
ص لبحوث العلمية الفائزة بجائزة
�
عدد خا
54
44
noticeable improvement on acid/clay process with respect to environmental
impact and its base oil yield is close to 72%. However, Viscolube no longer uses
this process on its own except for plants less than 10 thousand tons a year
1
. The
collaboration with Axens developed:
The Revivoil Process:
1, 3, 15, 87, 90, 91
Fig (9) sh ws a simplified flow diagram of this process while a more detailed
flow diagram can be fo
und on the company’s website
87
. In this process the first
stage is more or less the same as the original Viscolube process but the second
step is developed by Viscolube and is called thermal deasphalting (TDA). Axens
hydrogenation at high pressure step is added to make the difference to produce
Group II base stocks and raise the base oil yield to 79%
3
. Hydrogen saturates the
unwanted aromatics and treats all other contaminants of sulpher, nitrogen and
chlorine.
A “selectopropane” unit can be added to extra
ct DAO from the residue to improve
quality and yield to 95% (not shown in the diagram). The installation cost of such
a facility of 100 thousand tons a year is $35 million (2004) while the same plant
without the selectopropane would cost $30 million (2004) all ISBL (inside battery
limit). This information is obtained privately from a re-refiner. The process is
widely used in Italy (100 thousand tons a year), Spain (three plants at 20 thousand
tons a year each), Poland (80 thousand tons a year) and Indonesia (40 thousand
tons a year) with future expansion on the way.
The Snamprogetti Process:
1, 3
Fig (10). Patented in 1979, this is a solvent extraction process but later modified
to its present form to include a hydro-treating step. After settling and filtration,
the used oil is heated to 180
o
C and fed to a predistillation column to remove water
and light hydrocarbons at the top and a de-watered oil at the bottom. The next
step is a propane deasphalting column at 75-95
o
C and 355-710 psi. The wide
range is to cater for different compositions of used oil. The residue (mainly
asphalt) is drawn from the bottom. The propane solvent is recovered from the top
stream and the rest is heated again to 300
o
C and fed to a vacuum tower to produce
side streams of base oil cuts which are then hydrotreated to remove metals and
treat contaminates of sulpher, nitrogen and chlorine in addition to saturating the
aromatics.