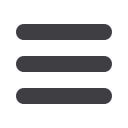
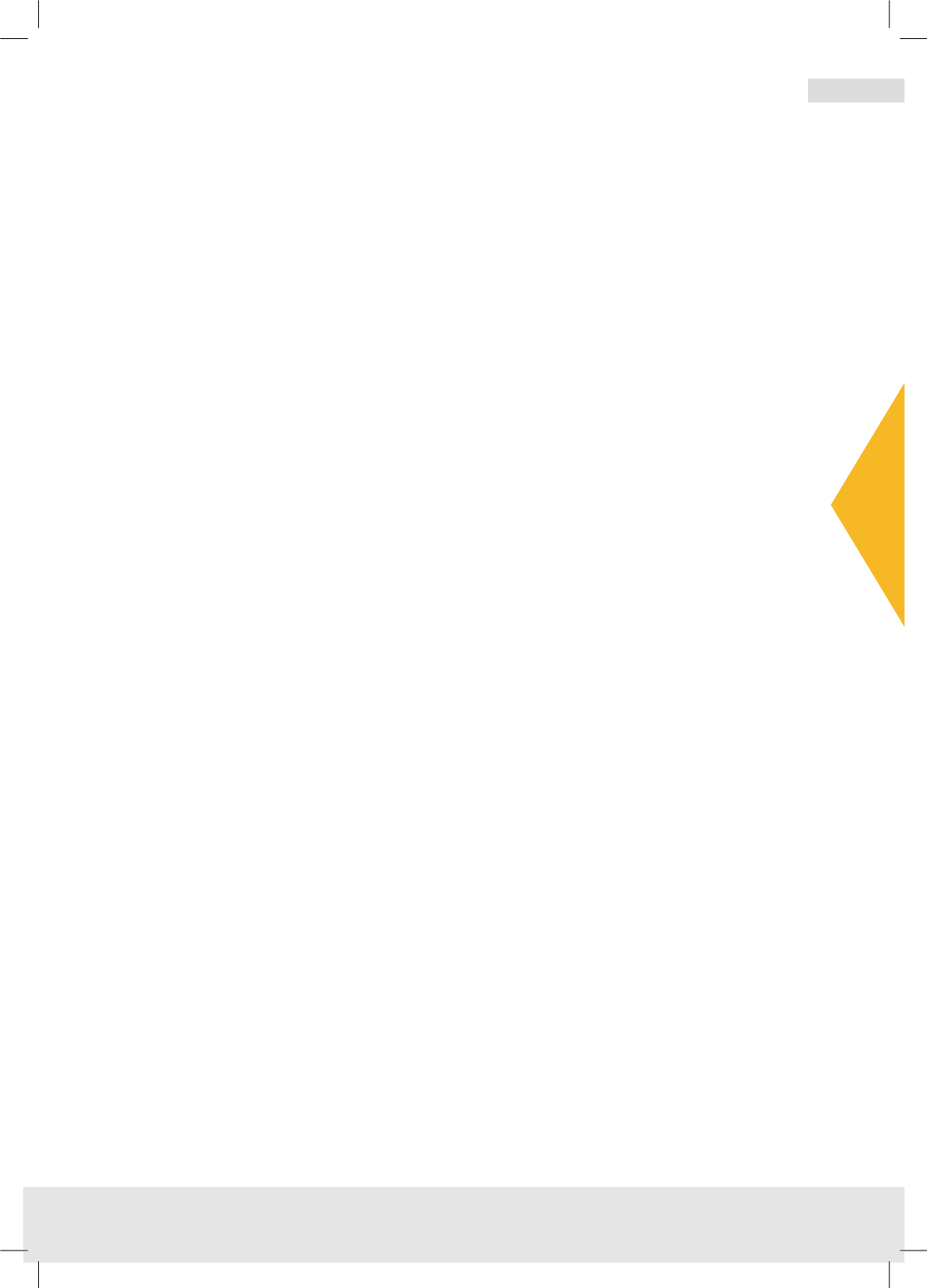
البحـث الثاني
141
2016
أوابك العلمية لعام
�
ص لبحوث العلمية الفائزة بجائزة
�
عدد خا
مجلة النفط والتعاون العربي
161
العدد
- 2017
أربعون
المجلد الثالث و ال
Re-refining of Used Lubricating Oil and its Economic and Environmental Implications
18
4 Types of used lube oils re-refining processes
Present day re-refining technologies provide a wide range of possibilities for recovery
of valuable base oil in a manner that is economically viable and environmentally
acceptable. As pointed out earlier in Chapter 2, many technologies were developed in
the late seventies and early eighties, which were based on existing oil refining
technologies such as vacuum distillation, solvent extraction and hydrotreatment. When
a re-refining project is contemplated, the investor is confronted to a wide variety of
choices when it comes to technology selection. The choice is no easy task as there exist
several competitive technologies and it is not within the scope of this study to analyze
all the available technologies. In this section, we will provide a general summary and
outline the key features of the processes with commercial applications.
4.1
Safety Kleen Technology
In 1998 the Safety Kleen process was used in the largest used lubricants re-refinery in
the world. The plant is located in East Chicago, Indiana with a capacity of 250000 metric
tons per year.
4.1.1 Process description
The Safety Kleen process is based on a combination of wiped-film vacuum distillation
and fixed bed catalytic hydrotreatment. Key processing steps are as follows:
Dehydration
The used oil is first dehydrated by evaporation to remove any water present in it.
Light ends recovery
The light fuels are removed in an atmospheric flash drum and collected
.
The vacuum
column/fuel stripper removes most of the fuel and heavier solvents.
Vacuum distillation
Next, the dewatered oil undergoes higher vacuum distillation to remove the lube cut of
feedstock while the by-products are used to produce asphalt extender.
Hydrofinishing
Then, the lube cut undergoes hydrotreating to remove residual polymers and other
chemical compounds. In this step, sulphur, nitrogen, chlorine, heavy metals and other
impurities are removed. The color, the odor and the corrosion performance of the base
oil are also corrected.