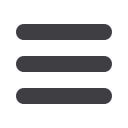
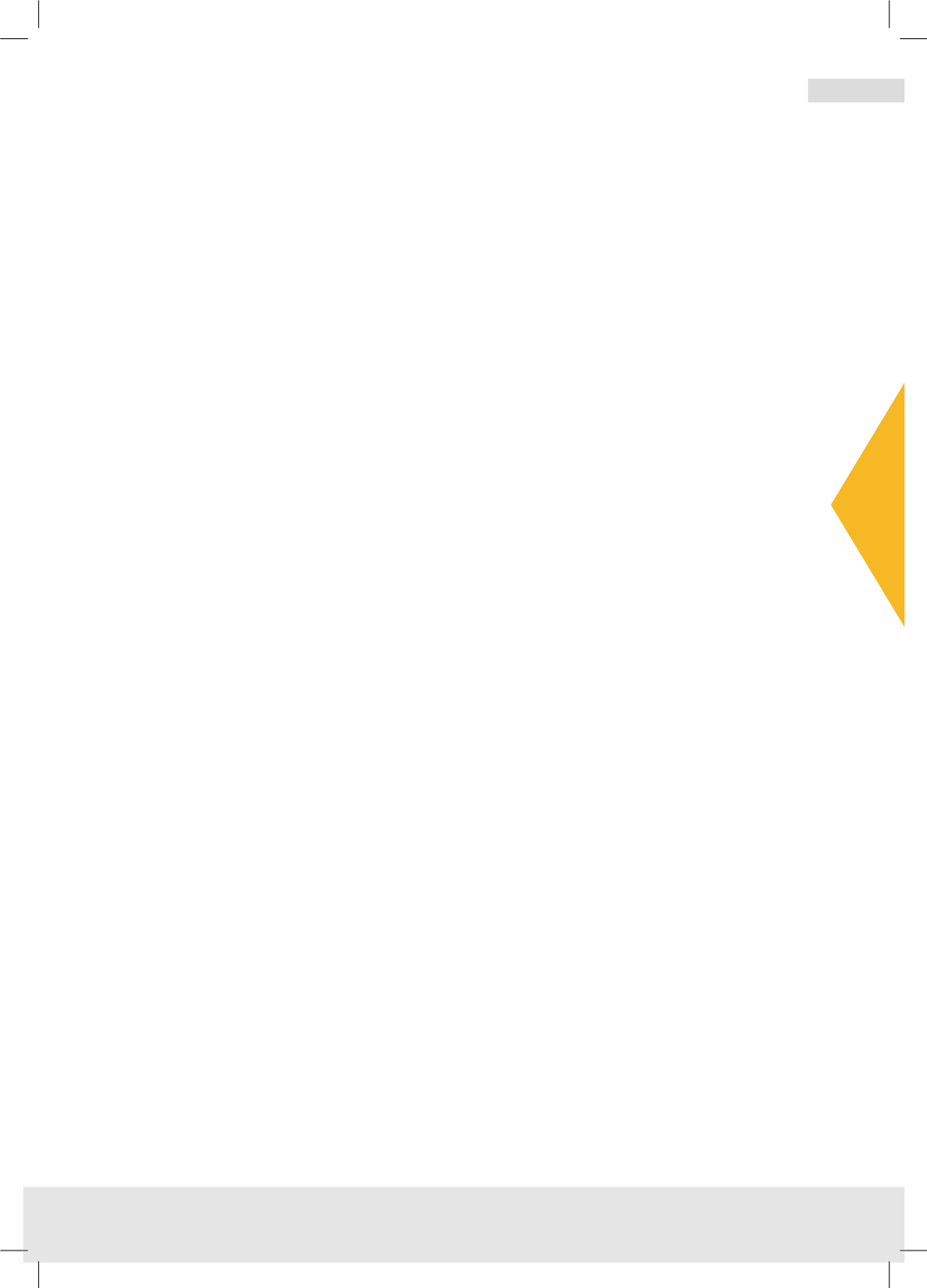
البحـث الثاني
147
2016
أوابك العلمية لعام
�
ص لبحوث العلمية الفائزة بجائزة
�
عدد خا
مجلة النفط والتعاون العربي
161
العدد
- 2017
أربعون
المجلد الثالث و ال
Re-refining of Used Lubricating Oil and its Economic and Environmental Implications
24
4.5.1 Process description
The process comprises the following steps:
Pre-flash:
The feedstock is heated (140ºC) and distilled in a column where the water and light
hydrocarbons are removed.
Thermal De-asphalting:
The dehydrated oil is distilled at 360 ºC in a vacuum de-asphalting column. The
asphaltic and bituminous products remain at the bottom.
Hydrofinishing:
The dehydrated oil is treated in the fractionation column( vacuum de-asphalting
column) where the asphaltic and bituminous products remain at the bottom and three
side cuts of different viscosity are obtained at the same time. Gas oil (VGO) is collected
at the top of the column. The base oil fraction is hydrotreated in the catalytic reactor to
eliminate unsaturated compounds, sulfur and nitrogen. The effluents from the catalytic
reactor are separated into a liquid phase and vapor phase. The liquid phase is stripped
with steam to eliminate the most volatile compounds. The re-refined base oil is obtained
at the bottom of the stripper.
Figure 12 illustrates the simplified process flow diagram.
4.5.2 Process features and drawbacks
This lubricating base oil has many advantages it is beneficial to health and the
environment as well as demonstrating excellent performance on the lubrication circuits
where it is used. The final result is clear oil with very low sulphur and aromatics
content.