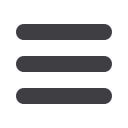
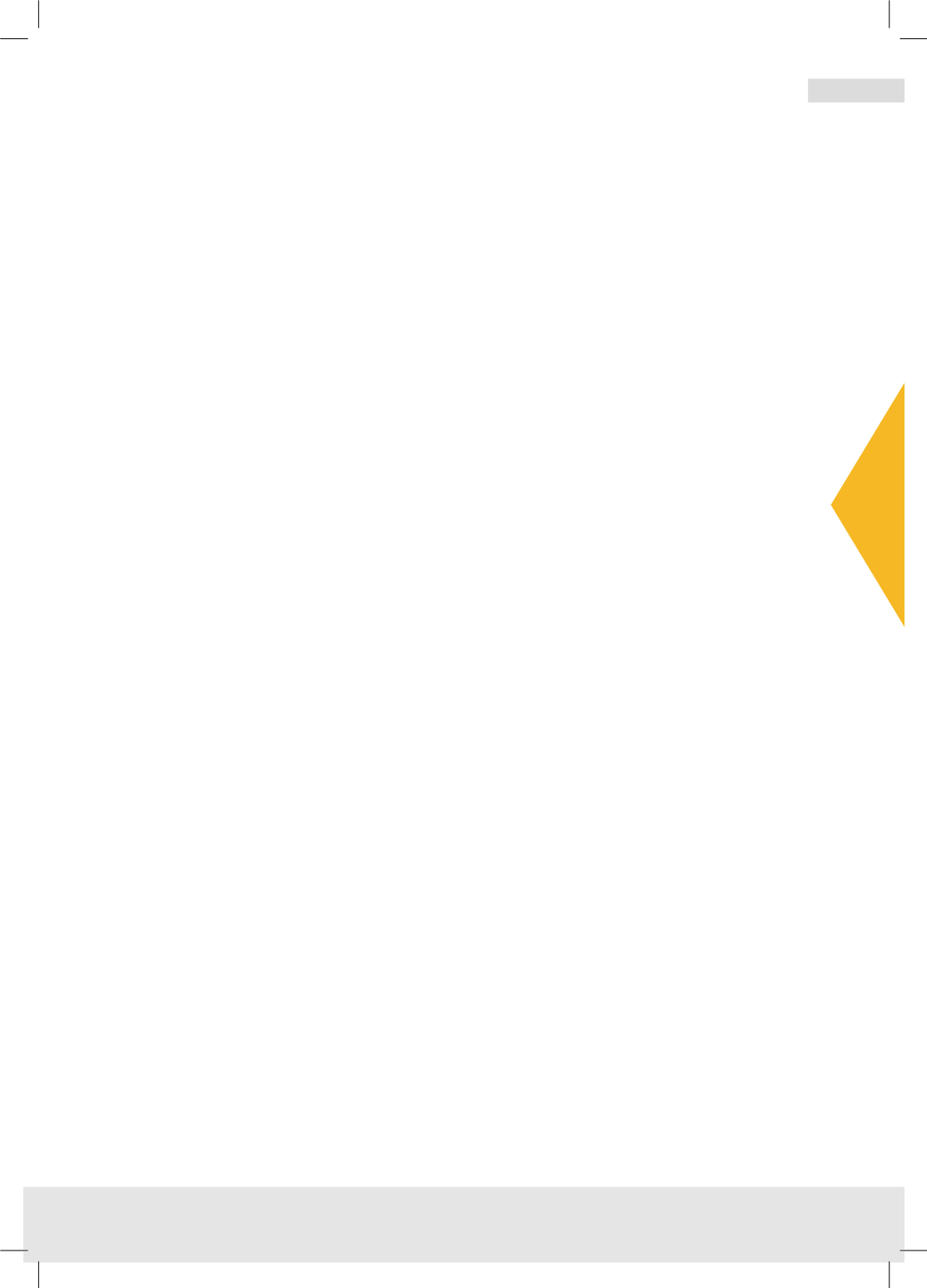
البحـث الثاني
149
2016
أوابك العلمية لعام
�
ص لبحوث العلمية الفائزة بجائزة
�
عدد خا
مجلة النفط والتعاون العربي
161
العدد
- 2017
أربعون
المجلد الثالث و ال
Re-refining of Used Lubricating Oil and its Economic and Environmental Implications
26
Gas oil stripping:
The dehydrated oil is sent to the gas oil stripping column working under vacuum. Gas
oil from the column overhead is condensed and sent to storage. Incondensable gases
from the vacuum system are sent to a thermal oil furnace.
Vacuum distillation:
The oil coming from the gas oil stripping column is introduced into a high vacuum
distillation column with thin film evaporator, where the separation of the lubricating
fraction and the residue takes place. The lubricating cut is then condensed and sent to
finishing while the asphaltic residue is sent to storage.
Finishing:
Finishing is done through chemical treatment for API Group I products or through
hydrofinishing in the case of API Group II lubricants production. Finished oil is then
sent towards the fractioning column and separated into two regenerated basic oils cuts
(150 SN and 500 SN) that are claimed to have the same specifications as their
corresponding new base oils. The column bottom is recycled towards the vacuum
distillation column.
The simplified process flow sheet is illustrated in Figure 13.
4.6.2
Process features and drawbacks
STP claims that process removes all the contaminants from the used lube oil and
recovers a base oil product as VGO or high quality lubricant which is in either API
Group I by chemical finishing or API Group II by hydro finishing. STP has
implemented several Re-refining Plants worldwide. The advantages of the process are:
High flexibility towards feedstock quality and composition
The lube oil recovery is more than 95% of the lubricant fraction present in the used oil.
The process is claimed to be highly competitive in terms of capital investment and
operating cost. It is also environmentally friendly as there is no use of acid and clays.
4.7
Probex process
The Probex (also known as Proterra) waste oil re-refining technology was patented in
1997 by Probex Co. This process is based essentially on vacuum distillation and solvent
extraction applied to vacuum distillates.