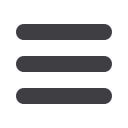
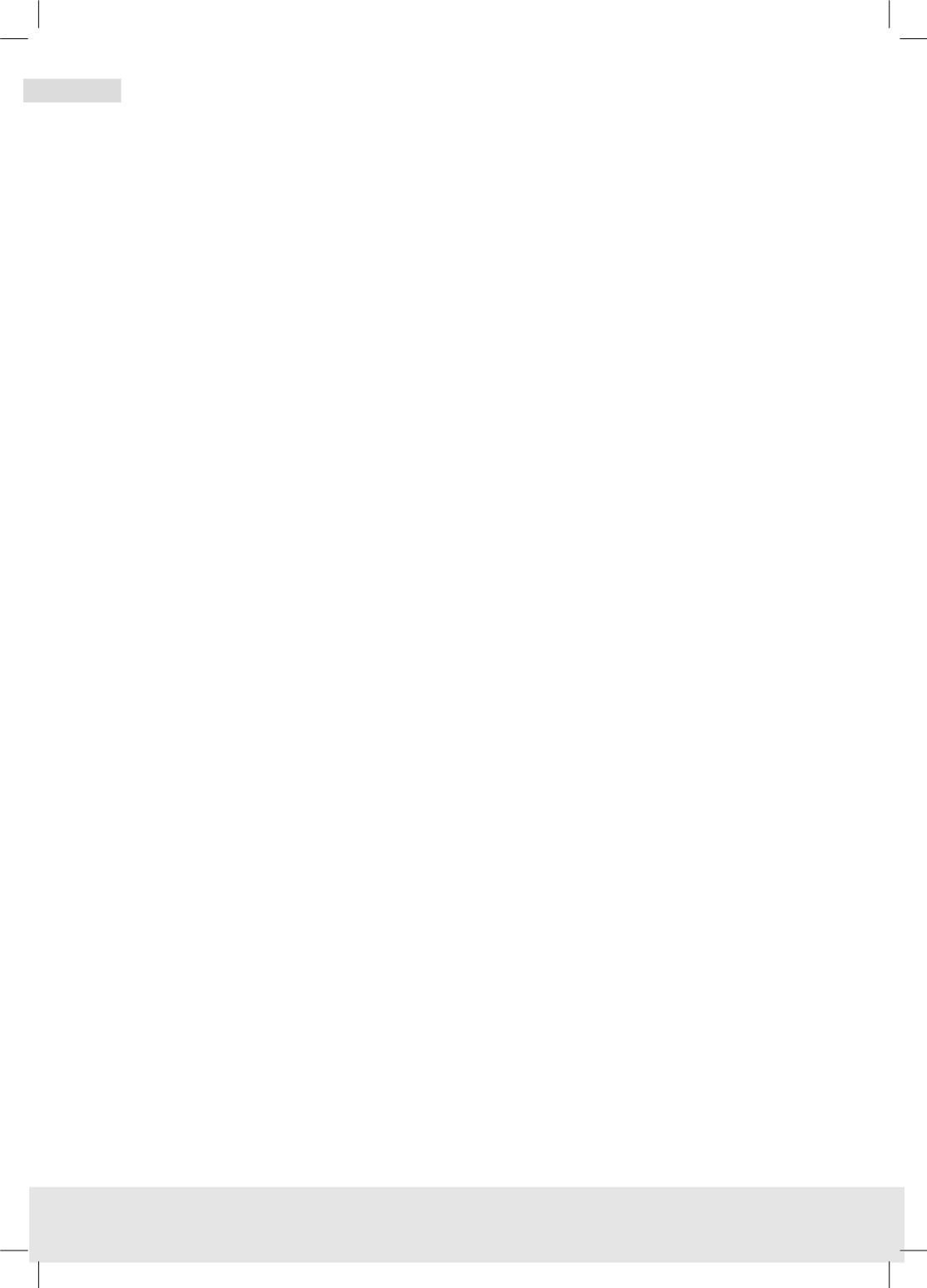
158
2016
أوابك العلمية لعام
�
ص لبحوث العلمية الفائزة بجائزة
�
عدد خا
مجلة النفط والتعاون العربي
161
العدد
- 2017
أربعون
المجلد الثالث و ال
Re-refining of Used Lubricating Oil and its Economic and Environmental Implications
35
Filtering:
The flash adjusted oil is then directed to a traditional vacuum distillation column. The
distilled lubricating oil product is a high quality base oil which, with a clay polishing
step, can be blended and marketed as a virgin quality lubricating stock.
4.12.2
Process features and drawbacks
It is claimed that with his process, it is possible to produce 70-75% base oil by separating the
water, degraded additives, wear metals and other contaminants in the oil.
Propane
extraction of the entire used oil stream results in a number of significant
technical/economic advantages over traditional re-refining technologies that do not
include a hydrogen treatment stage (Kajdas, 2013). The Interline technology eliminates
the need for wiped-film distillation (CEP, KTI, Safety Kleen) because the extraction
phase removes most of the used oil impurities that cause problems in traditional
distillation columns. As the process also eliminates the need for a hydrogen finishing
stage, it cannot handle waste oil contaminated with PCBs. The process operates without
extensive pressure and temperature (Giovanna et al, 2003). The operating and capital
costs are relatively low.
The simplified process flow sheet is illustrated in Figure 19.
4.13 ROSE/Kellog technology
4.13.1
Process description
The ROSE (Residuum Oil Supercritical Extraction) process was developed by Kerr-
McGee and sold to Kellog. This technology allows the treatment of used oil mixed with
grease. The basic steps of this technology are:
Solvent extraction:
In this step, the used oil is extracted with propane in two stages. In the first stage,
asphaltenes are removed by subjecting the oil to a specific temperature and pressure. In
the second stage, the de-asphalted solution of oil and solvent is subjected to a
supercritical temperature and pressure that facilitates the separating out of the oil and
solvent, which can then be recovered and reused in the cycle.
Vacuum distillation:
In this step,
the solvents are separated from the lubricants
by subjecting the
oil – solvent
mixture to vacuum conditions (40-200 ºC and 1-100 kPa)
Hydroprocessing:
Finally, the solvent-free extracts go through hydroprocessing to improve the content
quality.
The simplified block flow diagram is illustrated in Figure 20.